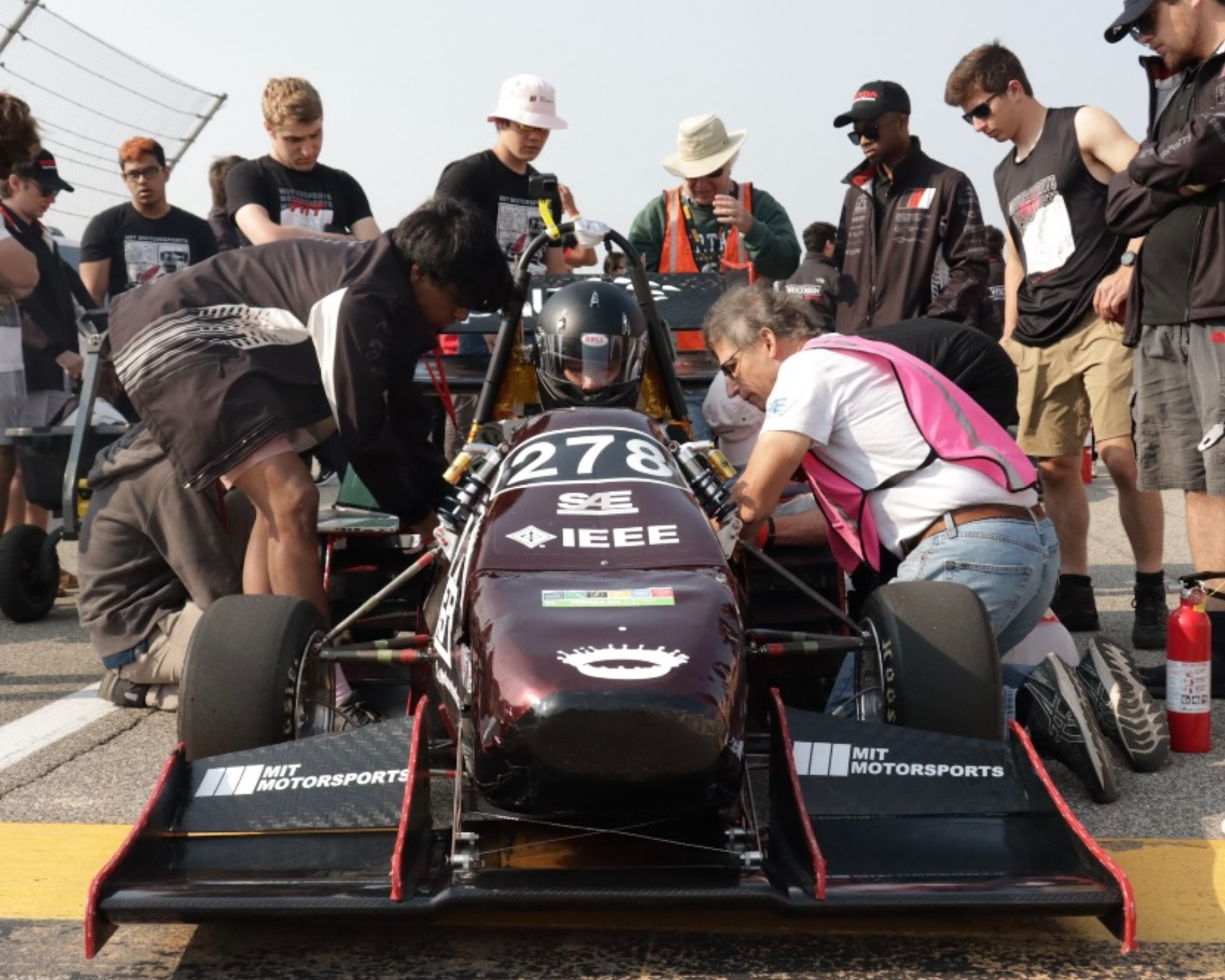
MIT Motorsports Mechanical Lead
For the 2023-2024 competition season, I joined the team’s Executive Board as Mechanical Lead. I was responsible for creating and upholding a team timeline, communicating with the other Executive Members, facilitating subsystem integration, managing team members, and preparing for competition. Over the year, I streamlined the new member onboarding program and increased the team’s size by 171%, enforced procedures to improve the documentation of design and build mistakes, led the team to pass Mechanical and Accumulator inspection, and competed in a dynamic event at the competition for the first time since 2019 (when our team was impacted by Covid).
Project Management
As Mechanical Lead, I oversaw the development of the chassis, suspension, 400V battery, powertrain, wheel packages, electrical boxes, ergonomics, mechanical safety systems, and 4WD system (an RnD project). While MY23 (Model Year 2023) was a continuation of the design cycle of MY22, there was a lot of remaining work to finalize the design, manufacture, and test.
I used a top-down approach to creating a team timeline, starting with the main subsystems (ex. battery, suspension, etc.). Then, I considered all their components and listed all the tasks that needed to be done for each. I estimated how long each task would take and organized their start dates by what could be done in parallel or had to be done in series. This led me to the team’s final Gantt chart.
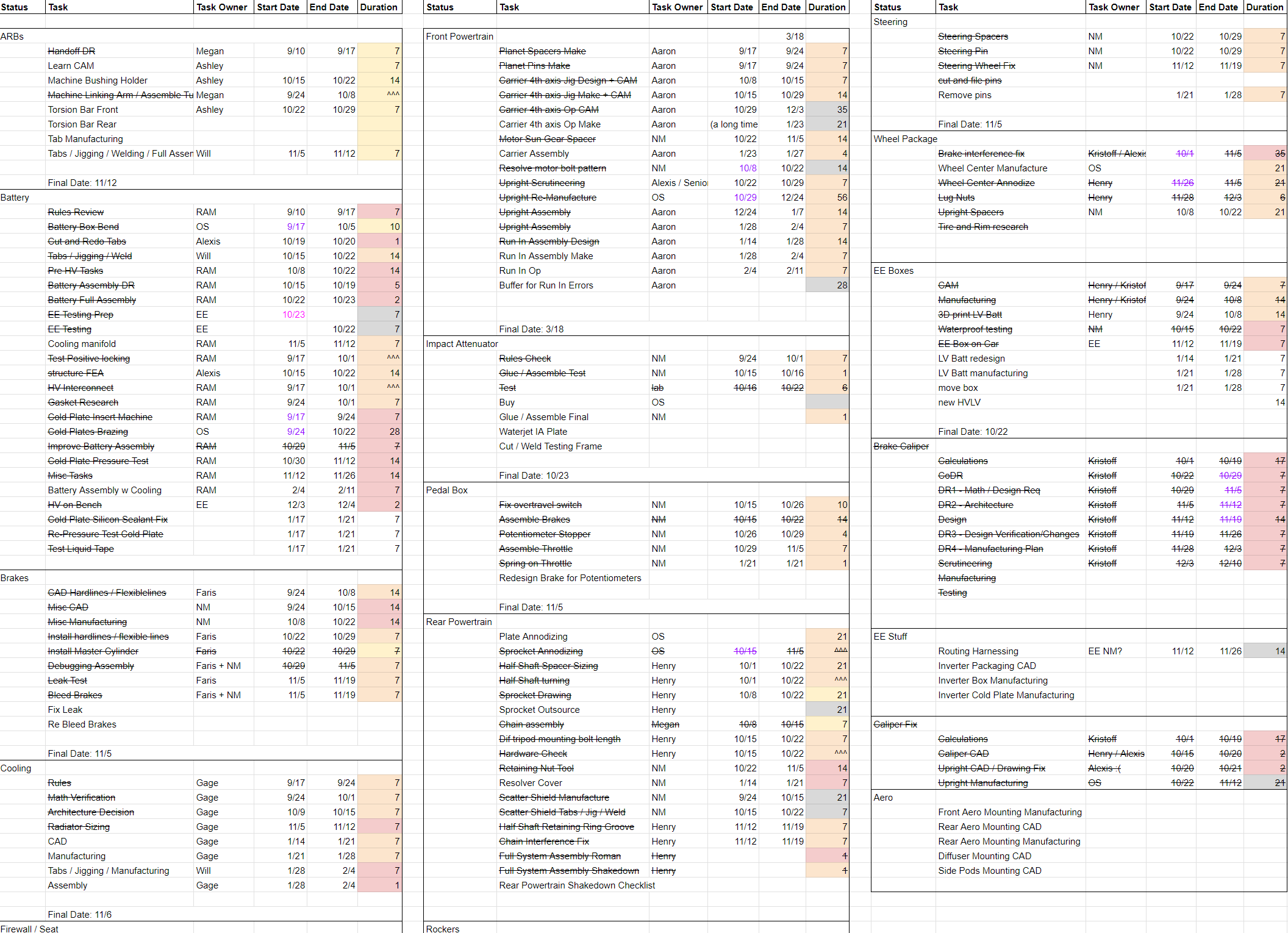
I confirmed the resource feasibility of the timeline by creating a separate chart of members and their tasks to ensure a person was not overworked (had multiple tasks during a single timespan) or underworked (had prolonged timespans of inactivity). I also used this chart to transparently convey work expectations to my members and, if needed, make changes to their allocated tasks to accommodate any time conflict (ex. study / exam dates, vacations, etc.). Through weekly 1-on-1 meetings with all my members, I consistently updated the team’s timeline and task allocations to effectively meet the team’s goals.

New Member Onboarding Program
In typical years, the Recruitment Lead organizes a project (separate from racecar tasks) for all new members to do in the fall. The goal was to familiarize them with the team’s internal logistics and CAD standards while learning basic machining processes. However, this year, I decided to center the new member’s projects around tasks for the racecar. This was because 1) we were continuing the design cycle of MY22 and had a lot of manufacturing tasks to distribute and 2) there were not enough current members to complete all the tasks. Besides this, I also believed that giving new members a project that directly contributed to the racecar would help increase their retention rate.
I chose tasks that were simple in scope and divided them into two subgroups: designing and manufacturing. I then grouped new members into teams of 4-5 depending on their interests and assigned tasks accordingly. Based on previous experience, I knew that in the beginning, a lot of new members leave as they settle into the school year and extracurricular activities. So, in the beginning, I met with only the teams weekly to discuss their progress and give technical guidance. Once the initial wave of new members dropped, I officially assigned the remaining new members to subsystems and held individual weekly meetings with them to provide more detailed guidance on more technically challenging tasks.
At the end of the year, the team had 12 committed new members, a 171% increase in retention compared to 2022 and a 400% increase compared to 2021.
High Voltage (400V) Battery
As the Mechanical Lead, I oversaw the development of MY23’s 400V battery. We made the battery from scratch using Sony VTC6 lithium-ion cells in a 12s7p configuration for each module. The battery had a total of 8 modules with a total maximum voltage of 403.2V and a maximum capacity of 8.5 kWh. The design of the battery was mostly finished from the year before, however, we needed to manufacture the enclosure, assemble the modules, improve the insulation, manufacture and test our custom cold plates for water-cooling, organize the high-voltage electronics, and assemble and test everything together.
Before being Mechanical Lead, I had no experience working with high-voltage components or batteries so, as a team, we approached the project with safety as our top priority. We began by reaching out to alumni who had experience working with high-voltage systems. Using their advice, we created an extremely detailed set of procedures including general high-voltage safety practices and procedures specific to our battery design including things to measure, what not to touch, an order of assembly operations, etc. Over the year, as we’ve fine-tuned our safety practices and resolved various mechanical and electrical issues, I’ve learned a lot about battery safety, design, and manufacturing. I am also very proud to say that we completed and tested the battery, passing Accumulator Inspection at the competition for the first time since 2021.
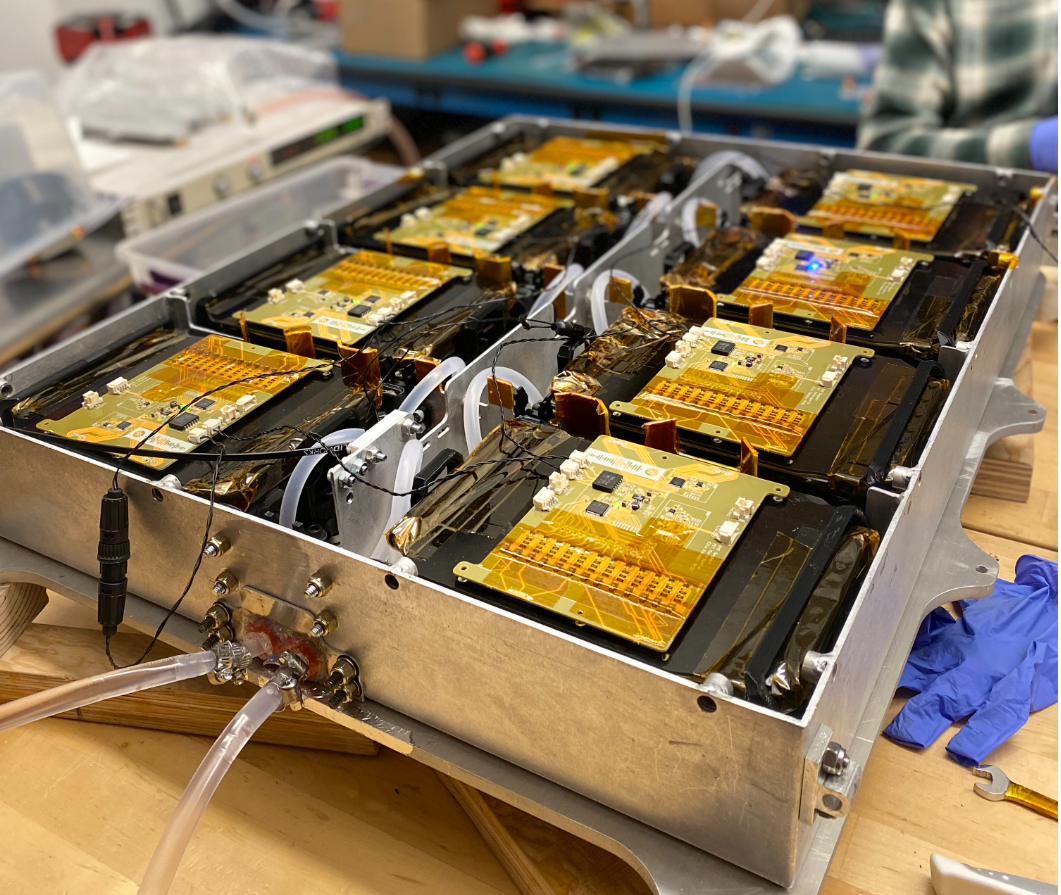
Formula Hybrid + Electric and Formula SAE Competition
In 2023, we competed in the Formula Hybrid + Electric (H+E) and Formula SAE competitions. Usually, we only compete in the Formula SAE competition, but because we didn’t compete in 2022, we wanted extra competition practice and experience. Numerous challenges arose as we discovered that Formula H+E has a different set of rules than the FSAE competition. We adapted our timeline and redistributed our task forces to account for this.
At the competition, our biggest challenge came during Mechanical Inspection where we found that our headrest tube thickness was too small. The only thing we could do was cut out the tube and replace it with a thicker one. With only one more day of Mechanical Inspection, we had to quickly organize the team to implement this fix. In just a couple of hours, we found a steel tube of the right thickness at a nearby store, cut and ground out the old tube, set up welding tools in our pit area, cut and cope the new tube to fit in place, drive our welder from school to the site, disassembled all electrical components on the car, and weld the tube with time to continue mechanical inspection that day. We passed the inspection the morning of the next day. In the end, we passed all technical inspections except for the brake test. While we didn’t compete in any dynamic events, participating in Formula H+E was integral to getting the team ready for the FSAE competition.
At the FSAE competition, we passed all technical inspections and competed in a dynamic event for the first time since 2019! It was an exciting accomplishment for the team.
Final Notes
This three-year journey through MIT Motorsports has been an invaluable learning experience for me. As a freshman who barely knew how to CAD and had no manufacturing experience at all, I could not imagine myself, in the end, leading such a wonderful team of talented engineers and completing such a technically vigorous engineering project. Because of this experience, I’ve learned how to apply engineering lessons from class in real-world applications and practice and improve my project management skills. I could see the effect my timelines and leadership have on the team, and I’ve learned to continuously reflect and improve upon myself. I’ve learned the importance of organization, communication, and constant attention to detail that’s required of a high-functioning team working to build an electric racecar.
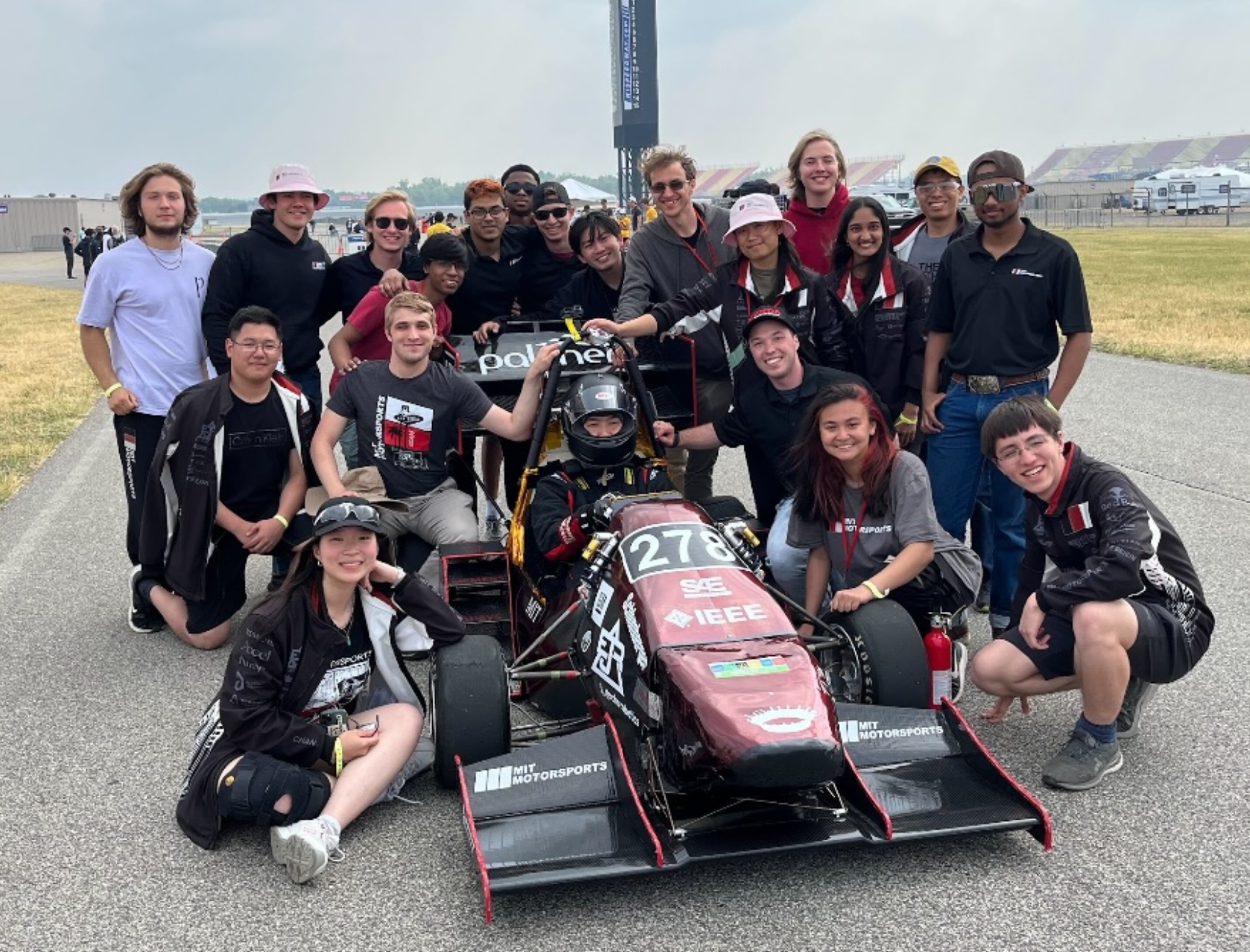