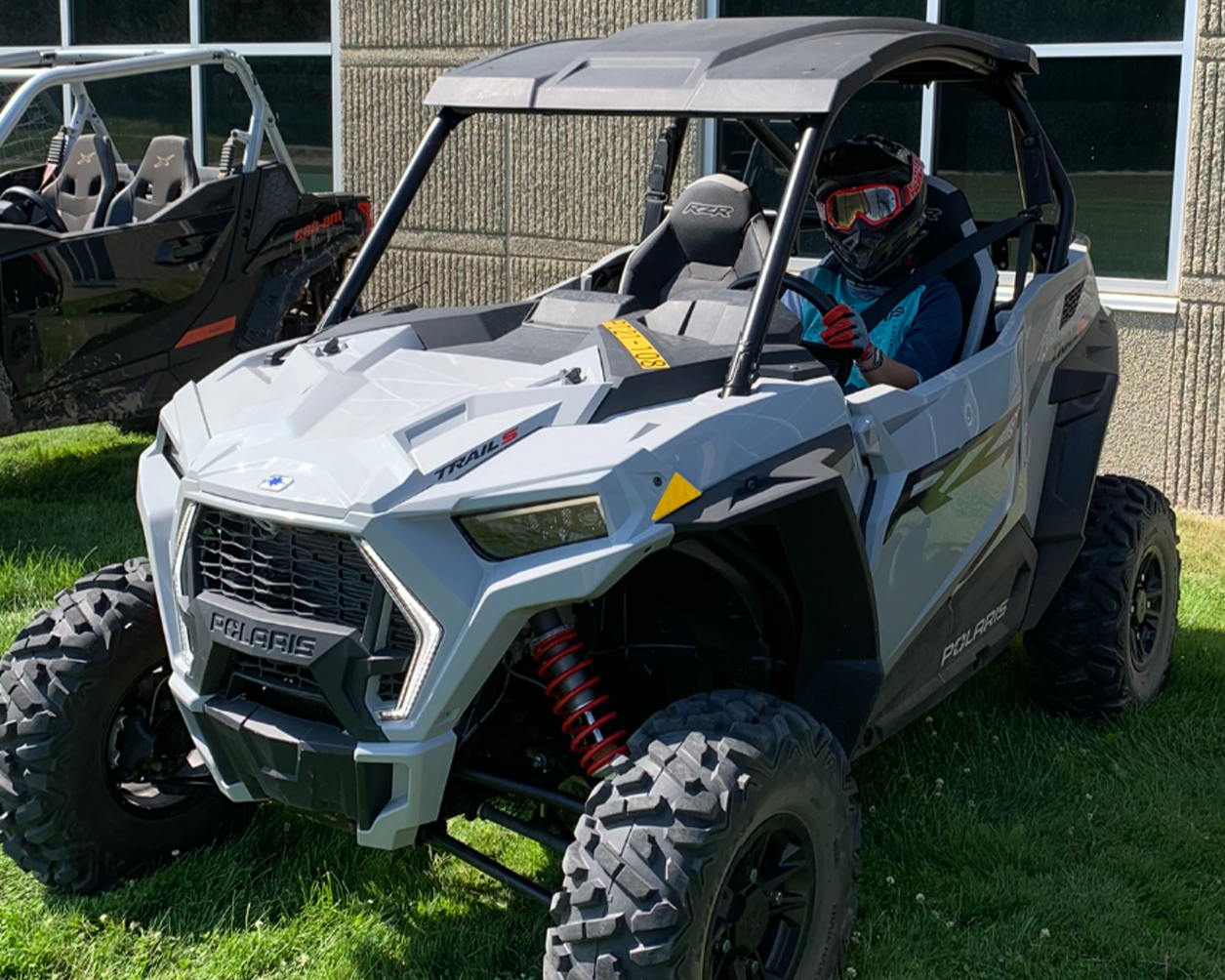
Polaris Internship
Propane and Linearization Procedure Documentation
To satisfy EPA Emissions Regulations, emissions tests must be conducted on all Polaris vehicles. This is done in their chassis dyno room where vehicles are driven in place to measure their emission. Instruments used to measure emissions periodically need to be calibrated in a process called propane and linearization checks. During these checks, known gasses are flowed into the dyno room and measured by the various instruments. My role was to document the procedures for performing the propane and linearization checks in a technical document following Polaris’s standards and in an easy-to-follow format for new employees to reference. I also cross-checked the propane and linearization procedures performed at Polaris with EPA’s regulations to verify that EPA’s standards were being met.
Engine Dyno Cooling System
The goal of this project was to design a portable cooling system for dyno-testing engines. It needed to be adaptable to all engine types and must fit within the dyno testing room. I began by talking to the engineers who managed the engine dyno tests and asked about their current cooling system, the controls they use, and which engines they tested. With this information, I sized two heat exchangers - a smaller one for the 2-stroke engines and a bigger one for the 4-stroke engines. I then designed a compact hydraulic loop with a reservoir, PID controller, filters, and heat exchangers supported by a simple 80/20 frame. While I didn’t have enough time to assemble the cooling system, I documented an assembly plan and BOM.
Engine Transportation Modules
The goal of this project was to design and manufacture a custom mounting system for holding engines safely during transport. To start, I defined design requirements using specifications from Cargo Securement Rules defined by the Federal Motor Carrier Safety Administration. According to the rules, cargo must withstand accelerations and deceleartions of 1) 0.8 g in the forward direction 2) 0.5 g in the rearward direction, and 3) 0.5 g in the lateral direction. Using these numbers and the weight of the engines, I sized a high-friction mat the engines can sit on. I then designed a custom 3d printed mold that allowed the engines to rest flat on the mat and to be ratchet strapped down to the pallet.